If you really want to irk a Chevy enthusiast, call the 348 V8 a truck engine. It’s sometimes said to be provocative but, more often than not, it’s promoted as gospel. Scour the Internet and you’ll find many references claiming the 348 was a truck engine. Is that true, or just an epithet?
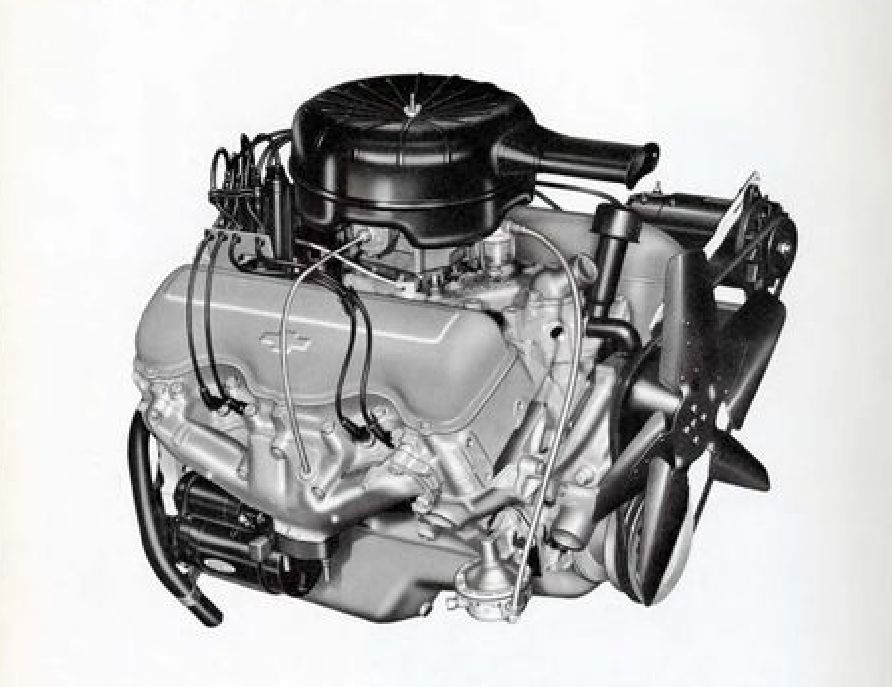
When Chevrolet introduced the small-block V8 for 1955, it was becoming apparent to market-watchers that the car-buying public was clamoring for more and more V8s. Upgrading engines for model-year updates was becoming an expensive proposition, as there had been rising demand for components like automatic transmission and air conditioning. Chevrolet wanted to plan for its future needs without expensive modifications that could also compromise the integrity of the engine design. Optimum low-end torque and mid-range performance was another consideration. “The W engine is different from the standpoint o[ being designed specifically to provide for future increases in displacement and compression ratio to meet yearly modification changes without the need for major redesign and the usual retooling required to provide the manufacturing equipment necessary to produce the engine,” wrote engineers in the article “Development of the Chevrolet W Engine: A New Concept in V-8 Engine Design” in General Motors Engineering Journal, Volume 5, Number 3.
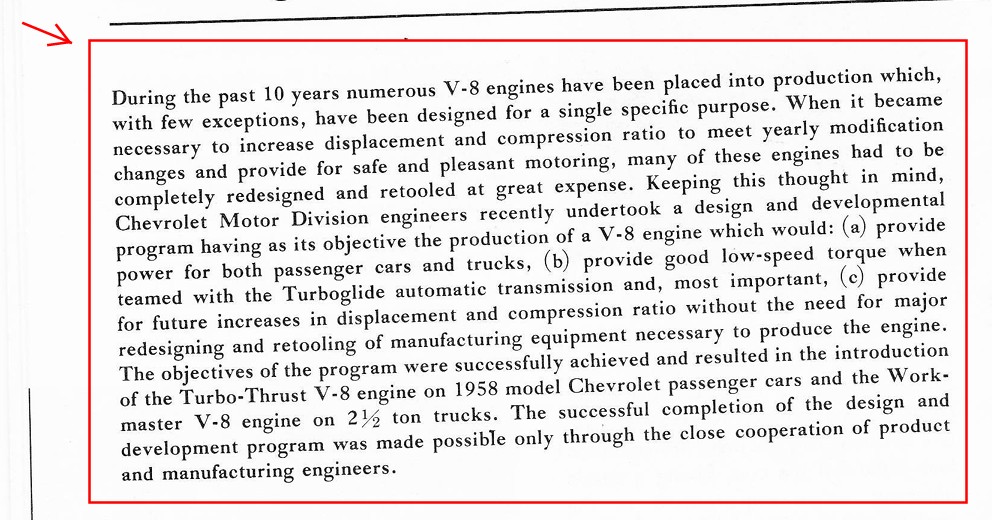
Initially, Chevrolet played with several small-block designs to investigate the viability of a engine larger than the current 265 and the 283 that was planned for 1957. Two different experimental small-blocks, both measuring around 300ci and featuring the same external dimensions as the current stock engine, were developed. For engine A, increasing the bore diameter required joining the bores, creating a casting problem and preventing complete coolant circulation around the cylinder; for engine B, new tools and equipment were needed for crankshaft machining. Additionally, both engines were limited in future increases in displacement and compression.
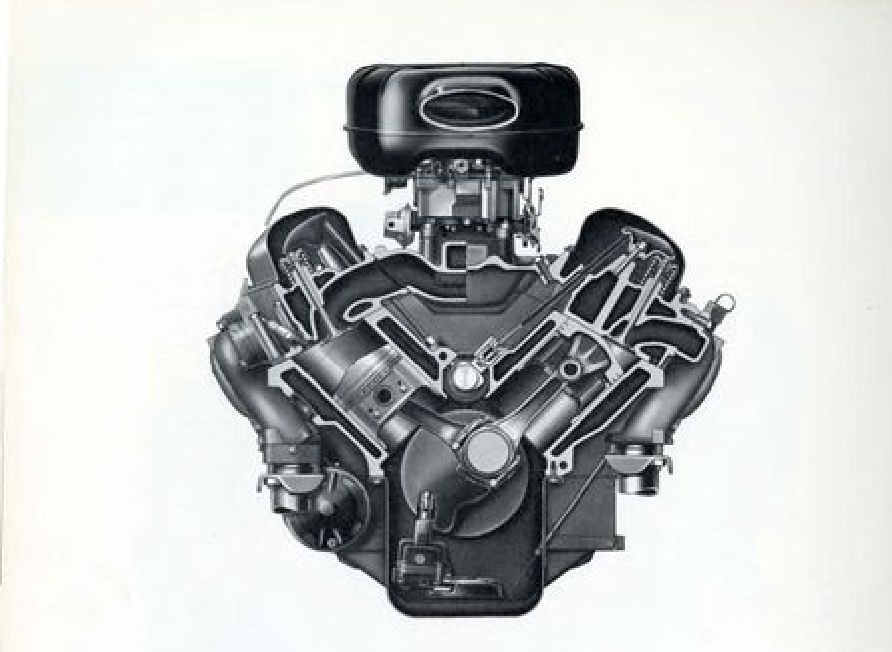
The future also anticipated requirements for both passenger cars and trucks. What if the design could be adapted to both? The production volume could warrant the investment in manufacturing facilities while reducing the capital cost per engine. The new engine would have room for future changes in displacement and compression without large retooling expenses, and the cost of added production could be amortized over a longer period of time.
Due to these considerations, the decision was made to start with a clean sheet rather than base the new V8 on the small-block. The new design became known as the W engine.
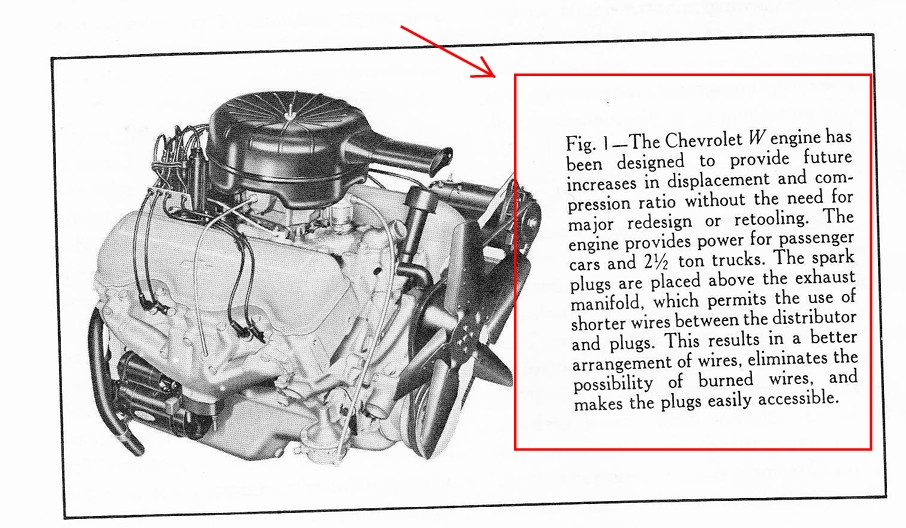
Five new ground rules were established (quoted from the aforementioned article):
- Adaptability to a broad range of displacement with a minimum number of different parts
- Overall dimensions compatible with anticipated space limitations of passenger car design
- Adaptability to a broad range of compression ratios to match the octane trend of future fuels
- Provisions for mounting accessories required for both passenger cars and trucks
- Flexibility in the use of machine tools to accommodate future engine modifications
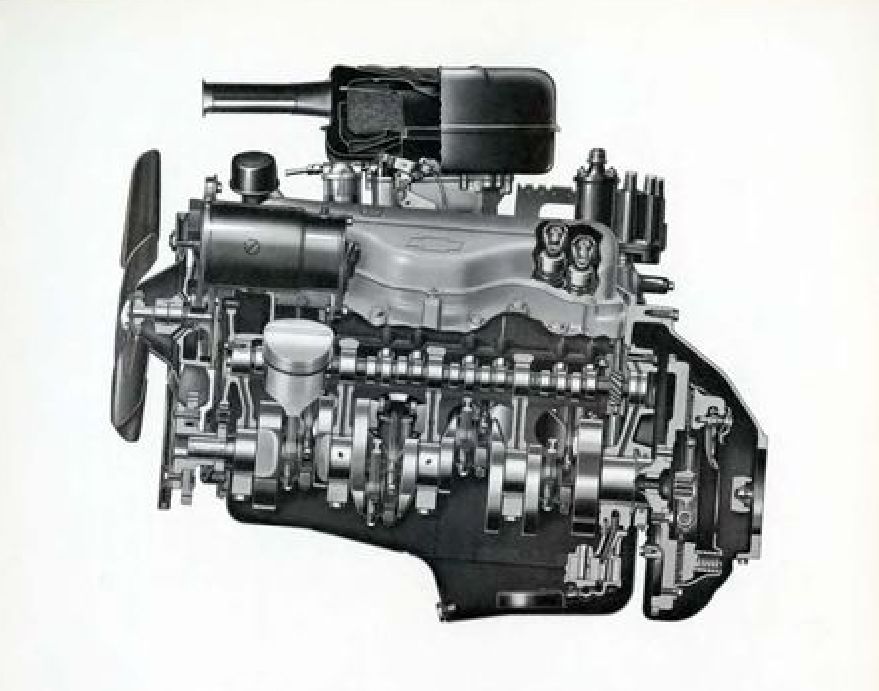
Chevrolet introduced the W engine (Turbo-Thrust for passenger cars, Workmaster for trucks) for 1958, becoming the first engine developed for both cars and trucks that met future, anticipated needs. It was produced through 1961, the same year the 409 was introduced. The 409 lasted through January 1965, upon which it was replaced by the 396 “Mark IV” big-block.
Now go tell your friends and change the trajectory of history!